System Identification
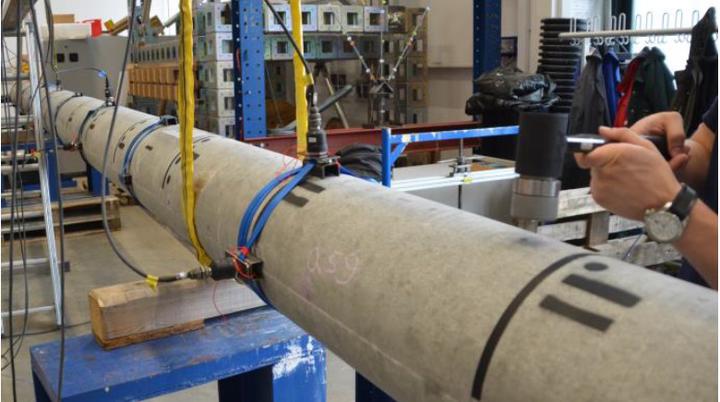
Noisy measurements from sensors can augment our mechanical models and improve our understanding of the actual state of our structures in reality: Are our input parameter and model assumptions correct or if there is any change in the system (possibly over time). This, in simple terms, represents the core objective of the Structural Health Monitoring (SHM) field, which aims to update and improve prediction models for structural assessment and maintenance. To achieve this goal, SHM employs different system identification and model updating techniques to learn from and incorporate noisy data into numerical and mechanical models. To this end, the use of machine learning methods as reverse-engineering probabilistic models has been quite beneficial in this field, particularly with recent advancements that have enabled the integration of these models with traditional mechanical models in a hybrid manner. This combination has led to a better understanding and improved prediction of the structural integrity of civil structures.
My research work in this field has primarily focused:
- On the use of Gaussian Processes (GPs) in a physics-informed manner for parameter estimation and prediction of beams and plates
- On the influence of material and geometric uncertainty on the dynamic properties of spun-cast prestressed concrete poles
On the phyisics-informed Gaussian Proceses for application to Kirchoff-Love plates and Timishenko Beams
This is an ongoing work that we primarily conduct with Gledson Tondo (a PhD student I co-advise). We employ Gaussian Processes (GPs) in a “physics-informed” setting (Raissi et al. 2017, J. Comp. Phys. 348) on the partial differential equations of Kirchhoff-Love plates and Timoshenko beams. The idea is to place a GP on the displacement field and apply the linear integro-differential operators of the mechanical plate/beam models to arrive at a probabilistic model that integrates both mechanical and data-driven models. Having noisy, heterogeneous data from sensors (e.g. strain and displacements), we are able to train this model while imposing physical relations between the measured quantities, and use it for prediction. In other words, we are able to infer probability distributions of the stiffness and physical quantities (e.g. displacements or internal forces) at places without any observations. The training is done using Markov Chain Monte Carlo sampling on the posterior of hyperparameters, yielding probabilistic estimates of both parameters and predictions. Additionally, we exploit the treatment of the physical quantities as probabilistic fields, and conditional entropy to develop an algorithm for sensor placement.
Two papers are in the works on this topic, one on Timoshenko beams (see this Paper), and another one is in works on Kirchhoff-Love plates. Below we show a couple of figures where the stiffness and prediction of physical quantities for both a plate and a beam are determined (the beam includes experiments!).

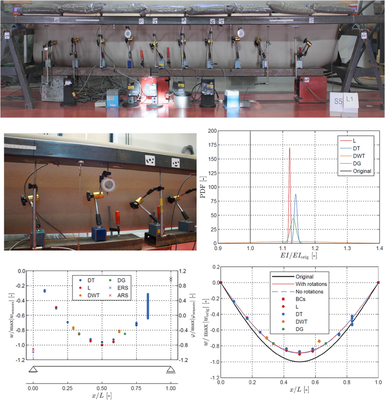
On the influence of geometry and meterial parameters on the dynamic properties of concrete poles
Our Pole Team of Research Training Group 1462 conducted an investigation into the impact of geometric and material uncertainty on the numerical modeling of a spun-cast pre-stressed concrete pole. In our experimental study, we carried out various tests to compare the parameter uncertainty with design code values, including: i) laser-scanning of the geometry, ii) concrete compressive tests on drilled cores from the pole, and, iii) dynamic tests with hammer excitation. We found that the pole’s thickness was approximately 17% higher, while the concrete compressive strength and Young’s modulus were roughly 62% and 15% higher, respectively, than the design values. To study the influence of these discrepancies, we created a finite element model, and compared the eigenfrequencies and modes to those determined experimentally from the dynamic test. We found that using the experimental thickness and material in the numerical model, yielded improvement from 7.5% to 1.2% difference in the first eigenfrequency. More information can be found in our Bautechnik paper (in German).
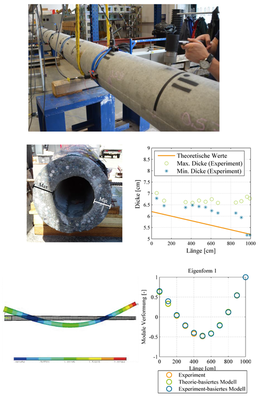